A proposed Assembly Bill (AB 1059) would repeal the 20 year old Wisconsin Department of Natural Resources Green Tier program. Although the bill is a long way from passage, the new law would likely eliminate the Green Tier program. This article explores potential options Green Tier participants might consider if the Green Tier law is repealed.
The table below compares Green Tier with a few other popular alternatives for organizations wishing to communicate their superior environmental performance to others. On the left, are the names of the programs including Green Tier. The top row shows the characteristics of each of the program types. A discussion of both the program types and the characteristics is below the table.
Program Type Characteristics | ||||||
Program Type | PDCA | Assurance | Global | Integration | Message Recognition | Cost to Implement |
Green Tier | X | Strong | X | Medium | Low | |
Green Masters | Some | Medium | Low | |||
ISO 14001 | X | Strong | X | X | High | Medium |
EMAS | X | Strong | X | Medium | High | |
CSR | None | X | Medium | Low -Medium | ||
CSR Verified | Strong | X | High | High |
Program Characteristics
PDCA – Plan Do Check Act continual improvement cycle? Most ISO type management systems are based on the PDCA model.
Assurance – Can the information be verified by an independent third party?
Global – Is this type of program globally recognized?
Integration – Does this program type integrate well with other protocols including ISO 9001, 45001 etc.?
Message Recognition – Are interested parties familiar with this type of program and messaging?
Cost – What is the cost to implement and operate this type of program?
Program types
Green Tier – A voluntary program modeled on the requirements of ISO 14001. Green Tier was passed into law in April 16, 2004 to help Wisconsin businesses communicate their superior environmental performance to interested parties. Green Tier is based on the principles of continual improvement that help organizations continually improve performance in many different areas. Green Tier also has an assurance component requiring participants perform periodic audits by an outside auditor of the organizations Environmental Management System (EMS). A Green Tier EMS can be easily integrated with quality and occupational health and safety management systems into the organizations overall business management system. Once accepted into the program, participants can communicate a strong message of superior environmental performance. Participants have up to one year to implement their EMS making this a relatively low-cost investment to implement the management system.
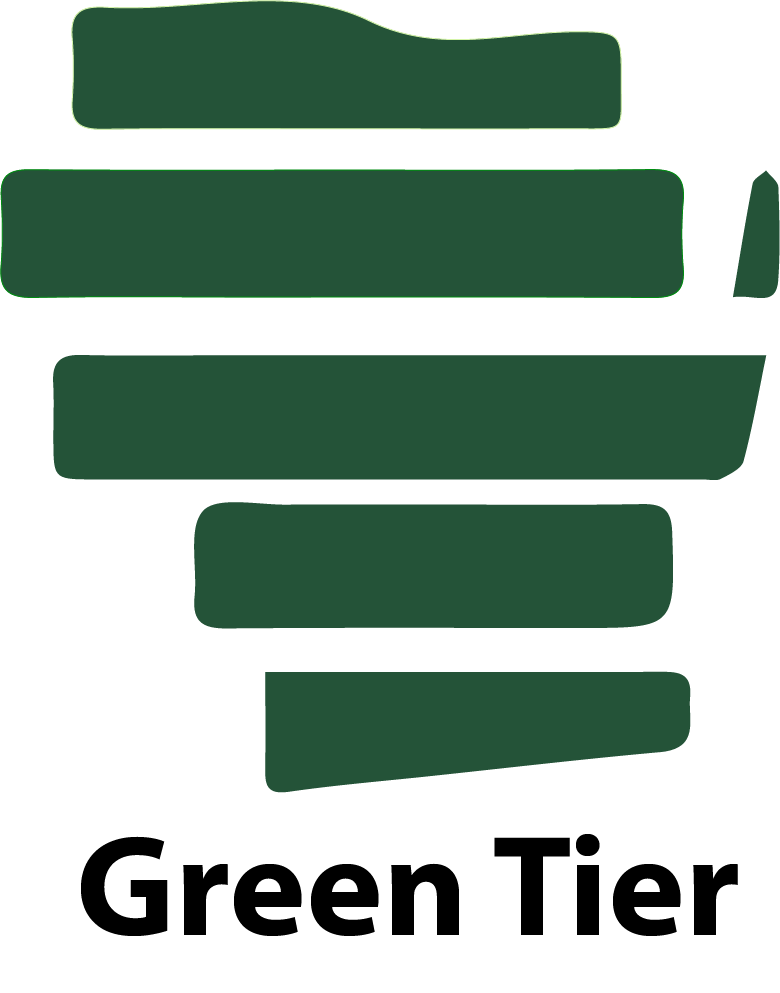
Green Masters – The Green Master’s Program helps businesses focus on sustainability issues important to them while contributing to bottom line and top line growth. The program also provides a framework to develop, integrate, and grow sustainable practices. It also helps record and track progress in the sustainability action areas. Participants in the Green Master program declare that they meet criteria established by the program. Green Master participants are recognized in four status levels.
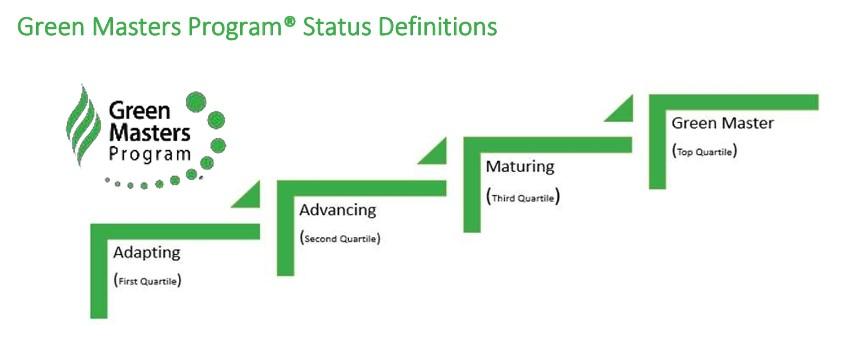
ISO 14001 – A globally recognized international standard based on the principles of continual improvement. The International Accreditation Forum has established a robust accreditation and certification program that sends a strong message of superior environmental performance to interested parties. ISO 14001 can also be easily integrated with other ISO management systems including ISO 9001 for quality management and ISO 45001 for Occupational Health and Safety Management Systems.
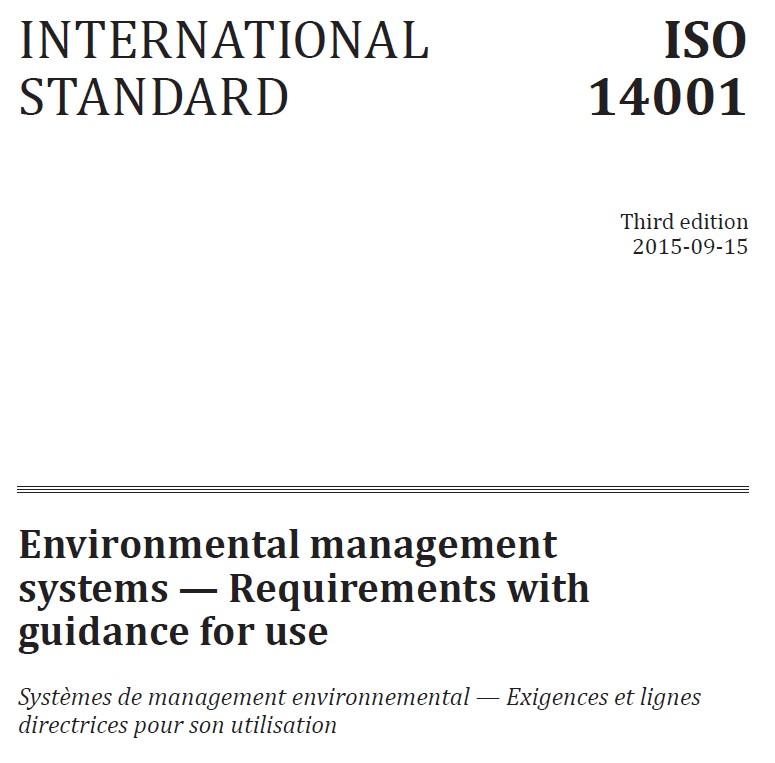
Eco-Management and Audit Scheme (EMAS) – EMAS is very similar to the Green Tier program for organizations in the European Union countries. It is a voluntary environmental management instrument, which was developed in 1993 by the European Commission. It incorporates ISO 14001 as a fundamental component and enables organizations to assess, manage and continuously improve their environmental performance. The scheme is globally applicable and open to all types of private and public organizations. In order to register with EMAS, organizations must meet the requirements of the EU EMAS-Regulation. Currently, more than 4,000 organizations and more than 12,700 sites are EMAS registered
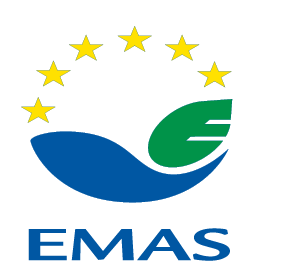
Corporate Sustainability Reporting (CSR) – Sustainability reporting has emerged as a cornerstone of corporate responsibility. Reporting can help businesses demonstrate their commitment to sustainable practices and transparency. The CSR trend is fueled by, government regulations, heightened stakeholder scrutiny, and a growing recognition of the significance of ESG performance for long-term business success. There are several popular CSR reporting standards each having their pros and cons. Here is a list of some most recognized:
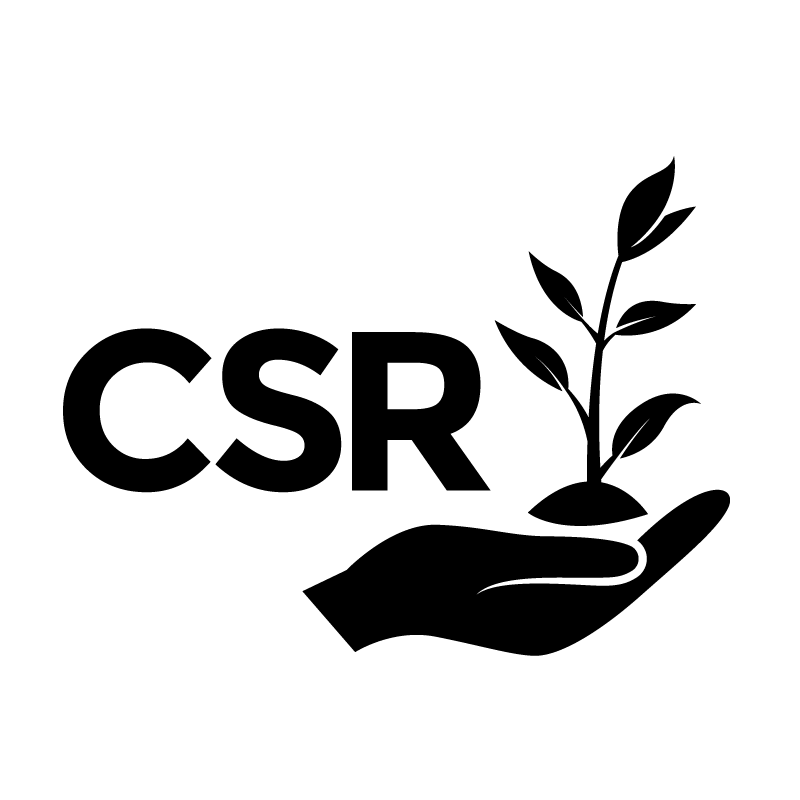
CSR reports are not based on a management system standard. Instead, they are categories or areas of sustainability that the organizations report. Organizations are not required to seek independent verification of the sustainability claims being made. This has led to criticism by users of the reports that the information is not reliable and may be considered “greenwashing”.
IASSB and ISO 14019 Sustainability Assurance
Criticism of unverified CSR reporting has lead to development of new standards for verification of sustainability claims in CSR reports. International Auditing and Assurance Standards Board (IAASB) has recently issued ISSA 5000 to help provide assurance to users of CSR information. The International Organization for Standardization (ISO) is also developing ISO 14019 for sustainability information verification and validation (VV). The ISO standards include a pathway for accreditation of VV bodies under ISO 17029.
Although Green Tier is unlikely to be repealed soon, we hope this information gives Green Tier participants a broader picture of ways to communicate sustainability information to those interested in your performance. For more information check out or Green Tier Services or you can contact us here or email us kalehner@envcompsys.com.