WDNR Green Tier Internal Audits
The WDNR Green Tier program requires participants to conduct periodic “outside” EMS audits to check that the system is functionally equivalent to ISO 14001:2015. By law, the minimum frequency of these audits is once every three years for Tier 1 participants and annually for Tier 2 participants.
Many organizations choose to perform WDNR Green Tier audits more frequently than prescribed by the Green Tier law. Longer than a year between audits result in increased risk to the organization. Postponing an annual physical from your doctor increases the risk that a medical condition will becoming a bigger medical issue.
WDNR Green Tier audits also provide important information to leadership. Reviewing Green Tier audit findings during management reviews allows leadership to evaluate how the EMS is functioning and if it is achieving the intended results. Leadership may miss important information when it reviews the results of audits only every three years.
Organizations that invest in their WDNR Green Tier audit program have better performing EMS’s and get a better return on their EMS investment. ISO 19011:2018, Guidelines for auditing management systems provides guidance for organizations wishing to improve their EMS audits. This guidance includes:
- How to establish audit programs
- How to conduct audits and report audit results
- What competencies auditors need to possess
- How to evaluate auditor competence.
Using the results of WDNR Green Tier Audits
WDNR Green Tier EMS audits evaluate audit criteria against audit evidence. Performing WDNR Green Tier audits ensures that “what should be is” and “what should not be is not”. Examples of audit criteria are requirements of Green Tier functional equivalence, compliance obligations such as permit requirements or requirements such as WDNR universal waste and hazardous waste regulations. They can also be internal requirements the organization has set for itself.
A robust EMS audit process and procedures coupled with effective corrective action process to address audit findings is critical to the effectiveness of am EMS. If the audit process or the corrective action process is weak the EMS may not be able to achieve the intended results of the EMS.
WDNR Green Tier Audit Corrective Actions
Green Tier audits are fundamental to superior environmental performance, but audits alone do not make changes that improve performance. Audits simply identify conformance and nonconformance to the requirements of Green Tier and the organizations internal requirement for the EMS.
Audits can be good news or bad news. If an organization is performing audits and find nothing but “good news” that is not especially noteworthy to leadership. Things are going along well, according to plan, and there is no identified need for action. When audits find nonconformances or bad news, this is good news to leadership because the audit has identified things that need to be fixed.
If organizations are either not performing effective audits or no audits at all this is bad news for leadership. Leadership has no way of knowing if the EMS is performing as planned. “No news” is bad news.
Audit nonconformance findings are good news and a source of EMS performance improvement. Audit nonconformances are not evidence of failure or reason to find fault. Doing so will create fear of the audit process within the organizations and increase the difficulty in gaining employees trust and cooperation with the audit process.
To benefit from the results of audits organizations also need to fix the nonconformance problems the audits discover. Performing audits and then being unable to correct the problems discovered is often a bigger problem than not performing audits at all. An example is an audit of regulatory compliance status that discovers a potential noncompliance. Uncorrected findings later discovered in a regulatory agency compliance audit could result in enhanced “knowing and willful” criminal penalties. Finding a potential noncompliance problem and not fixing it is worse than not finding it in the first place. To reduce risk, organizations need to take corrective action on audit findings in a timely fashion.
Some organizations struggle to get traction on their corrective action process for two primary reason.
- A clear process or workflow for performing corrective action has not been defined and or communicated by the organization.
- The organization has not established a systematic way to keep track of and report on if and how the nonconformance are being addressed.
WDNR Green Tier Audit Corrective Action Workflows
Corrective action workflows for audit nonconformance should be a team effort. Teams should follow several sequential steps collaboratively and reach consensus on each stage in the workflow. The last stage of the workflow is verification of effectiveness of the corrective action.
This team approach is similar to the collaborative product design process used by industries to develop products. The design process has desecrate points in the process called gates. Design teams agree that each step was completed before the design process can progress through the gate to the next stage
The purpose of this design review workflow is to ensure the design process is proceeding in a systematic fashion and to minimize the potential for design flaws that will become apparent in the production or use stage of product or service.
Figure 1 is an example of a corrective action workflow with approval gates and stages.
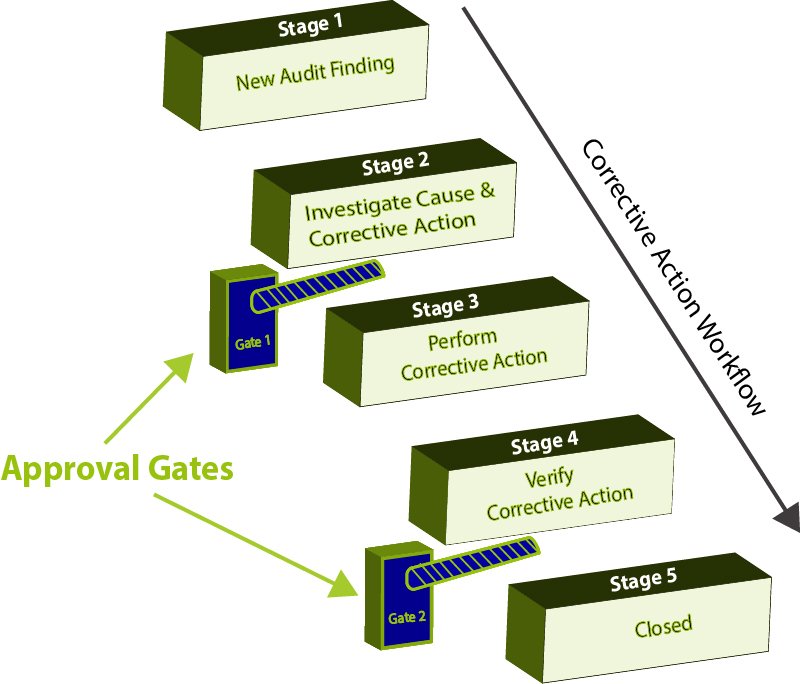
Gates separate some of the stages in the corrective action workflow. The number of approval-gates in the corrective action process can vary depending on the organizations’ needs. Stages in the corrective action workflow can include:
Stage 1 – New (Contain and Assign)
Recognition of the problem is the first step in the corrective action workflow. Recognition can occur as the result of an audit or incident. How the workflow proceeds after recognition depends on the gravity of the problem or incident encountered. The team leader or gate keeper needs to quickly decide what type of problem it is such as:
- Easy to Fix – We understand the problem cause and we can just fix it because it is unlikely to recur
- Not so easy to fix – We do not fully understand the problem but believe that the cause and solution can be discovered without commitment of substantial resources at this stage.
- Difficult to fix – This type of problem needs significant resource (horsepower) to address it with skill.
The preliminary evaluation will determine the size and competencies of the team needed to address the problem.
The team should consider Immediate steps to contain the problem (stop the bleeding) and what that containment should be. Placing lables and dates on the universal waste containers corrects the audit finding.The person assigned to the corrective action task should not delay implementation.
Stage 2 – Investigate (Cause and Corrective Action)
Cause analysis
Putting a band aid on the problem with a short-term correction alone will not address the underlying problem cause and the nonconformance is likely to recur. Determining the cause of a problem is necessary to find a solution that fixes the problem and prevents recurrence. The team should investigate why the problem happened in the first place.
Root cause analysis is a huge topic and there are many approaches to doing a cause analysis, but sometimes asking “why did that happen?” several times can help identify the underlying cause of the problem (5 why analysis). Other problems can be more complex and require more horsepower than a 5 why analysis can deliver. These types of problems may need more sophisticated cause analysis techniques such as Six Sigma (DMAIC), 8 Disciplines (8D) or others.
Corrective Actions
The root cause of the problem helps the team discover an effective corrective action that will prevent the problem from recurring. The team should reach consensus that the proposed corrective action is appropriate to the cause before the corrective action is implemented. This will improve the likelihood that the corrective action will fix the problem in a way that it will not happen again..
Corrective action solutions that are based on one individual’s perception of the root cause and how to fix that problem often oversimplify both the cause and the solution. The tendency is for individuals to hurry the process and close the nonconformance as quickly as possible. This leads to weak root cause analysis which in turn compromises the selection of an appropriate corrective action.
If the corrective action process is not monitored in a team setting the assignee is more likely to close out the issue (get it off their desk) as soon as possible. A team approach to the corrective action process that use approval-gates can help avoid this consequence. Approval-gates encourage robust cause analysis.
The following is an example of poor cause analysis and proposed corrective action for the audit finding that universal waste containers were not properly labeled and dated.
- Proposed Cause – “The employee had not been trained in how to properly package and label the universal waste”.
- Proposed Corrective Action: Train the employee in how to properly package and label universal waste.
This cause analysis simply repeats the finding. It does not describe why the problem happened in the first place and the proposed corrective action is more of a correction than a corrective action. Implementing this action will not ensure that the same problem does not happen again.
Root Cause Analysis
Figure 2 shows the results of a more appropriate cause analysis of the universal waste packaging and labeling nonconformance.
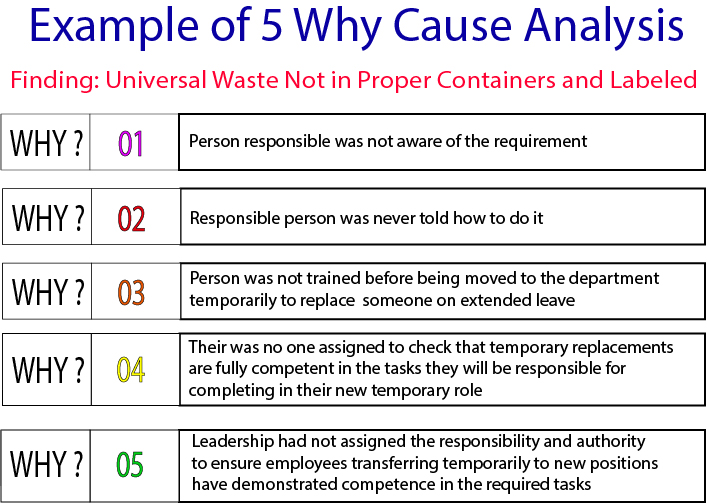
Once the root cause is identified an appropriate corrective action can be proposed that will prevent it from happening again.
Often there are several options for corrective actions that fix the problem in a way that it does not recur. Some might have potential to be extremely effective but are costly to implement. An example might be to outsource the universal waste management to a contractor that comes to the site daily to check that the universal waste is being management correctly. This is highly effective and can transfer some of the risk of universal waste management, but it is expensive to implement. Before the corrective action is approved the team needs to decide if the proposed corrective action is appropriate for the cause.
An appropriate corrective action decided by the team for this problem and cause might be something like:
- Leadership will direct the HR department to develop a training matrix that shows competence required for all jobs including temporary fill in positions.
- The HR department will develop a process(es) that require(s) employees to demonstrate competence to do a job before the employee can be assigned to that job including temporary fill-in positions.
The team should reach consensus that the proposed corrective action is appropriate for the root cause before it is implemented. Once approved the actions should be implemented without delay.
Stage 3 – Perform (Corrective Action Implementation)
The team implements the corrective action after it is approved by the team and its leadership. One individual can implement a simple corrective action quickly. Complex problem solutions may require development of a project plan that assigns team members tasks. Task assignee’s need to accomplished these task by established dates. The team monitors progress on the tasks and periodically reports to the team leaders.
Stage 4 – Verification of Effectiveness
Verification confirms that the agreed upon corrective action was implemented as planned. It also confirms that the corrective action implemented was effective and fixed the problem in a way that it will not happen again.
Corrective action verification is usually performed by internal or external auditors during regularly scheduled or other audits. Others in the organization or on the team can perform the verification but it is important that the verifier be independent to the implementation process or the area where the verification is occurring.
Stage 5 – Closed
Team can close the corrective action after it has been verified. The team may need to invest additional effort if the verification finds that the corrective action implemented did not fix the problem. The team may need to re-investigate the cause and to re-propose and implement another corrective action.
Communicating and Tracking Corrective Action Status
A significant stumbling block that organizations sometime encounter when addressing nonconformances is the absence of a method to communicate and track the status of completion of the corrective action. Information about corrective action status has traditionally been paper based or electronic. These systems assign a corrective action task to someone to investigate and complete.
The team leader passes the physical or electronic copy of the corrective form to team member responsible for investigating the cause and proposing a corrective action. Then the paper or electronic copy is passed to other team members to add information or it is returned to the team leader for review and approval.
Assignee’s can misplace paper or electronic copies of corrective actions. Paper-based tracking systems require large three ring binders to store the completed corrective action forms and associated supporting documentation such as pictures or other evidence of completion of the corrective action. Electronic documents are often individually stored in folders located on the organizations servers or in the cloud.
With paper-based systems, communicating the overall status of corrective actions to leadership requires a labor-intensive process of thumbing through the three ring binders and manually recording the status of the corrective actions. Individual documents stored on servers or in the cloud have similar problems. Sorting through individual folders and files takes time to to find important information about the corrective action program. Use of electronic spreadsheets can help here but create other problems that limit the effectiveness of this solution
Corrective Action Tracking Database Apps
Industry 4.0 revolution will soon fundamentally and significantly change almost all business. This revolution is helping organizations store data optimize equipment and operations using the cloud environment. Organizations will be able to access enormous amounts of information with a click. Affordable cloud-based applications that track corrective action progress progress of are now becoming available to all types of businesses. Some of these application are easy to use and allow quick access to trends that inform management decisions.
The heart of these cloud based applications are databases that organize and store information. They help communicate the status of corrective actions to team members and leadership. These applications make it easy to monitor the approval-gate process and communicate with team members via automated emailing functions when the status of a corrective action changes or is approaching a due date. Correcttrack.com is a cloud based application that helps organizations keep track of Green Tier audit findings and improve the effectiveness of the corrective action process.
Conclusion
WDNR requires Green Tier participants to periodically audit their Green Tier EMS. Audits confirm the organization has established and is operating a “Functionally Equivalent” EMS that results in superior environmental performance. They are the critical “checking” part of an effective functionally equivalent EMS. If performed with skill the audit results can provide important information that the organizations leaders need to determine if the EMS is achieving its intended results.
Ensuring the results of audits are addressed in a timely fashion is critical to an effective EMS. This is especially true for nonconformance and noncompliance audit findings because findings that go unaddressed or with poor corrective actions increase the risk to organizations than if audits had not been done at all.