Introduction
Skillful performance of concise management review meetings can dramatically improve management’s perception of the value of the EHSMS. The key to successful management review is distilling important information about the performance of the EHSMS to a point where it is actionable by management and presenting this information in a timely manner. Here are a few Does and Don’ts for successful management reviews:
Does
• Use regular periodic general business review meetings to present selected EHSMS inputs.
• Make sure the inputs are concise, well thought out and include recommendations for action.
• Include financial information such as Return on Investment calculations with recommendations.
• Keep a log of the dates each of the required inputs was discussed and records of the details of the presentation and any outputs from management.
Don’ts
• Conduct management review infrequently (only annually).
• Forget to record the results (outputs) of management review
• Ask management what they think should be done. It is the management review presenters’ responsibility to make EHSMS recommendations for improvement upon which management can act.
• Try to cover everything at once.
Discussion
The following is a brief discussion the Management Review Does:
Use regular periodic general business review meetings to present selected EHSMS Management Review inputs.
Good managers and leaders recognize that organizational change happens in increments. That’s why most organizations conduct regular periodic meetings of the management staff to review important attributes of business performance such as production issues, staffing, financial performance, new predict development and sales. These meetings are used by management to keep in touch with many of the key performance indicators management uses as a basis for deciding what incremental interventions are needed to keep the business healthy and prosperous.
These meetings are a great opportunity for the EHSMS manager to briefly get top managements attention about specific important EHSMS issues and propose potential incremental changes to improve performance. The notion that EHSMS Management Review is only needed infrequently (for some organizations only annually) can result in significant delay in management’s recognition of potential improvement opportunities and delay in realizing the benefits of the improvement. More frequent reviews also keep management informed on the progress of execution of recommended changes (outputs of management review). Figure 1 is a example of how you might create a schedule for performing portions of management review during regulator business review meetings.
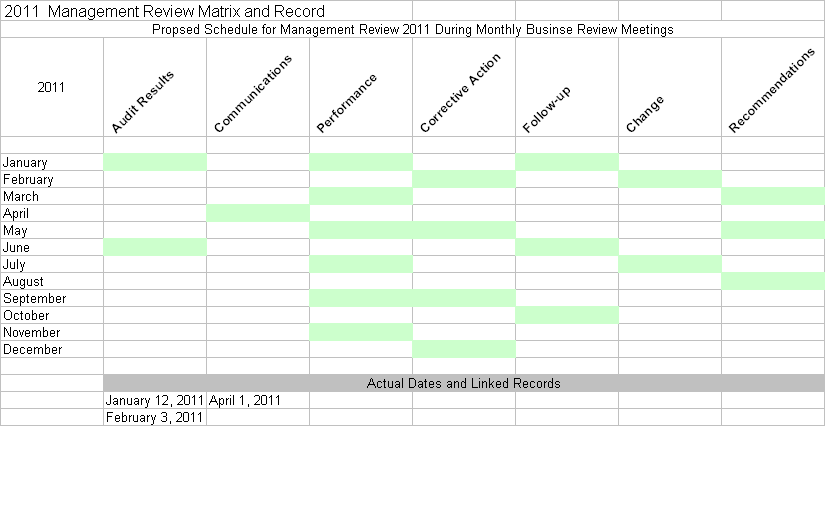
Figure 1
If management review is only conducted infrequently top management at the organizations will not know if the interventions they have approved are effective. It may be another year before they get any feedback on whether the recommended improvement was implemented and if it had an effect on performance.
Make sure the inputs are concise, well thought out and include recommendations for action.
Doing more with less is the reality of businesses today. Human resources including management resources are scarce and top managements time is a precious commodity. Therefore it is important to be able to quickly cover the important points about an EHSMS issue in a way that will result in an action (a decision by top management). Make sure that at recommendation for action is included at the end of a brief presentation of the facts of a particular issue. If you simply present the facts of an issue without a specific recommendation management may not act. Proposing a specific recommendation as a potential solution to an issues encourages management to make a decision.
Include financial information such as Return on Investment calculations with recommendations.
Improvements in the EHSMS are good but, if they require an investment of financial or human resources management will likely care a lot about what they will get out of that investment. Putting a monetary value on the benefits in terms of return on investment helps management justify it. Proposed investments in the EHSMS should cash flow within the time period that management would consider for other investments.
The ROI for recommendations for improvements in environmental performance are easier to calculate than health and safety improvements because they are more measureable. Re-lighting a warehouse with energy efficient bulbs is an good example because it is fairly easy to calculate how long it will take to recover the investment.
Calculating ROI for Health and safety improvements is a bit more difficult because it involves estimating the relative risk of something bad happening and the consequences of that event. When presenting health and safety recommendation you should include a recommendation for what risk level should be acceptable and what it will cost to achieve that reduced risk level. Management then needs to decide if the recommend risk reduction is acceptable and worth the investment of financial or human resources.
Keep a log of the dates each of the required inputs was discussed and records of the details of the presentation and any outputs from management.
Records of the results of management review are valuable to show evidence of management commitment to the EHSMS. They can be used to show external auditors the organization is conforming to the requirements of ISO 14001 and OHSA 18001 clause 4.6. They may also be valuable should an incident occur that is investigated by a regulatory agency (USEPA or OSHA) or if there is a civil action involving an injury case.
A matrix or table like Figure 1, showing what parts of the EHSMS were reviewed when (during regular business review meetings) can help you retrieve the records of what was discussed and what decisions were made. Keeping a brief accurate record of the issues discussed and the outputs from management and then linking these records to the dates on the matrix will help in locating specific management review meeting minutes when they need to be retrieved.
Conclusion and Recommendation
The management review part of an EHSMS is a powerful tool which enables incremental improvements in EHSMS performance. Done with skill, management review can improve the perception by management of the value of the EHSMS. Integrating the management review function with normal business review meetings helps management address import EHSMS issues in a timely incremental fashion.
Take a look at your management review process and decide if it is helping sustain the continual improvement process and the effectiveness of the EHSMS. If not, maybe it is time to think about re-engineering the management review process to make it more relevant to the organizations performance improvement efforts.